The vibrating screen includes a circular vibrating screen, a linear vibrating screen and a resonant screen, and the first two are often collectively referred to as an inertial vibrating screen. Although they differ in their working principle and structure, they all have the same main components, namely vibrators, screen boxes, transmissions and vibration isolators.
1. Vibrator The vibrating screen has pure vibrating vibrator, bearing eccentric type and pulley eccentric self-centering vibrator. Since the latter makes the vibrating screen structure simple, easy to manufacture and long in service life, it has been widely used in practice.
The linear vibrating screen has two kinds of vibrators, box type and barrel type. However, some new vibrators, as long as the structure is slightly adjusted, can make the vibrating screen linear or circular motion, which can be called a dual-purpose vibrator. The resonant screen consists of two nearly equal vibration masses that make up the excitation system. These vibrators will be detailed below.
In addition, there is a simple vibrator which is composed of an eccentric block directly mounted on a motor and is called a vibration motor. It can be mounted directly on the screen box without the need for a transmission. Vibration motors have been developed since the late 1980s and have been used in medium and small screening equipment .
2. Screen box The screen box is composed of screen frame, screen surface and its fastening device. The screen surface and its fastening device have been described above. The box frame is composed of side panels and beams. The side plates are made of 6-16mm thick steel plates, and the beams are made of steel pipes, channel steel or I-beam; they can be joined by riveting, welding or high-strength bolts. The manufacturing process is complicated when the riveted structure is used, but the adaptability to the vibration load is good. The welding structure process is simple, but the weld seam is complicated, the internal stress is large, the weld seam is easy to crack when subjected to strong vibration, and even the component is broken; for this reason, tempering treatment can be used to eliminate the internal stress. Generally speaking, the welded structure is suitable for small and medium-sized vibrating screens, and the high-strength bolts and ring groove rivets are suitable for large vibrating screens because of reliable connection and easy assembly of the screen frame on site.
3. Transmission The vibrating screen generally adopts a V-belt transmission device, which has a simple structure and can select the rotation speed of the vibrator arbitrarily, but the belt is easy to slip during operation and the screen hole is blocked. Some use a coupling to directly drive the vibrating screen, so that the vibrator speed can be stabilized and the service life is extended, but the vibrator speed cannot be adjusted. High performance gearing systems are also currently used.
4. Vibration isolation device Vibration isolation sieves commonly used vibration isolation devices include coil springs, leaf springs and rubber springs. The spiral spring has a compact structure and a small outer shape, and the obtained rigidity is small, the vibration damping performance is good, the fastener is not required and the work is reliable; but the disadvantage is that the lateral rigidity is small, and the sieve is prone to transverse vibration. The advantage of the leaf spring is that the lateral stiffness is large, and the transverse vibration can be eliminated. The disadvantage is that the outer shape is large, the installation is difficult, and the fracture accident is more. The advantage of the rubber spring is that the outer shape is small, but the rigidity is large, the vibration isolation performance is good, and the disadvantage is that it does not adapt to large amplitude and large dynamic load. Due to the large amplitude of the vibrating screen, a cylindrical coil spring is generally used as the vibration isolating device.
400-500KG/h Production Line
400-500KG/h Production Line
As leading manufacturing in powder coating field,we have 30 years rich experience.Our R&D team developed OPTIMIZED SERIES" which comes in two type(E type & D type) and NEWTEC SERIES.Including lab production line,Premixer,extruder,cooling belt and mill system. The products can satisfy the capacity from 10kg/h-1000kg/h.
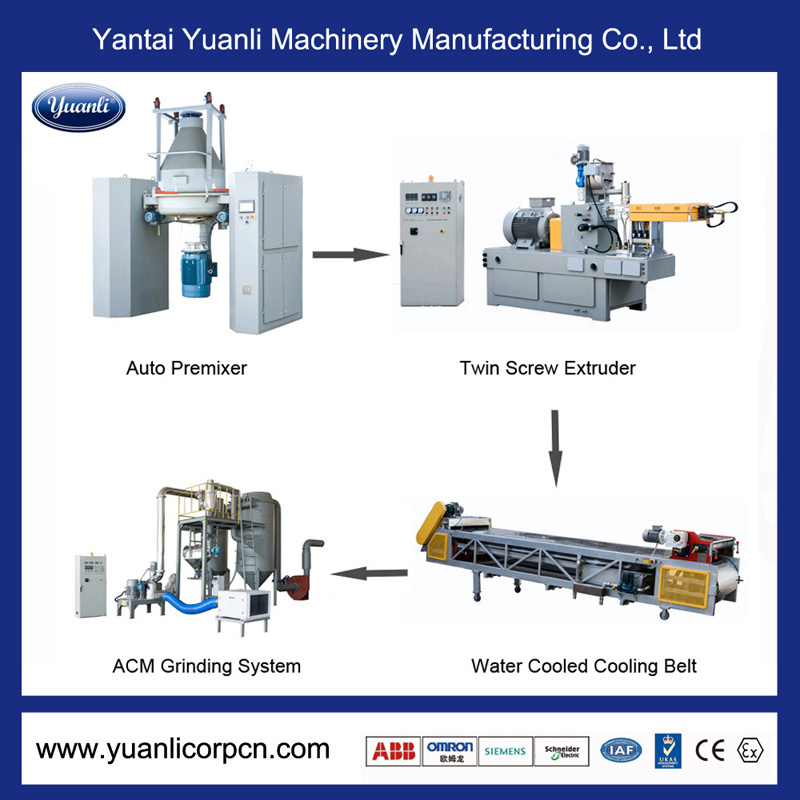
Our Advantage & Service:
-Technical Support Online Service Provided
According to customer's requirement, we provide layout (plant designer), excellent mechanical engineer, excellent electrician, etc.
-On-site Training Service Provided
In customer factory, we provide all kinds of training, including installation, commissioning
-Long-term Maintenance Provided
In the area of maintenance, we offer needs-oriented and standardized maintenance packages, such as the overhaul of components, gearboxes, in order to guarantee the safe and economic operation of plant and machinery.
-Spare Parts Replacement and Repair Service Provided
Providing spare parts for all kinds of powder coating processing equipment in long-term. And can provide tailored made spare parts according to customers' requirements. Ensure advanced craft, good material and high precision.
-Formulation Provided (our advantage):
Some customers are worried their final products if can get best result, we have our own formulator (Engineer for powder coating formulation) who is testing and updating the formulation according to customer requirement all the time. And have very good experience for the formulation to support customer to make different effect powder coatings.
We can supply all Powder Coating Raw Materials( polyester resin, epoxy resin, barium sulfate, gloss agent and so on) in the formulation.
Siemens Motor Powder Coating Production Line,White Powder Production Machine,Wrinkle Powder Production System,Powder Coating Machine Installation
Yantai Yuanli Corp Ltd , https://www.yuanlicorpcn.com